智能电动机保护器自动检测系统设计
品慧电子讯: 为了提高智能电动机保护器产品精度及可靠性,基于数字电子技术、模拟电子线路、单片微型计算机及上位机语言,开发了一套自动检测系统。介绍了系统的软硬件设计,并进行多次测试。测试结果表明,该系统能对智能电动机保护器自动施加信号,以检验其精度、保护功能及附加性能,自动判别测试结果是否满足技术指标要求,且检测结束后能实现测试数据的自动保存与打印。与常规的人工测试系统相比,具有检测效率高、测试过程规范、自动化程度高、准确度高、通用性强、测试数据管理便捷等特点。该自动检测系统已在公司流水线上正常运行,被证明是切实可行的。
本文作者:郑月节 陈江 李海全 蔡磊
作者单位:
1. 江苏安科瑞电器制造有限公司,江苏 江阴 214405)
2. 中国海诚工程科技股份有限公司,上海 徐汇 200031)
0引言
智能电动机保护器具有远程通信接口,模拟量输入输出、开关量输入输出,与传感器、PLC、PC等组成控制系统,能实现电动机运行的远程监控[1], 适用于煤矿、石化、冶炼、电力、船舶、污水处理等领域的自动化管控、民用建筑的智能管理。由于用户需要功能多样、保护功能复杂,所以其可靠性涉及到多方面 指标,为了确保产品的质量,智能电动机保护器的各项指标在出厂之前均需要经过严格的检测。目前,对其检测采用手动方式,故存在检测工序繁琐、工作效率不 高、可靠性低、检测流程不规范、检测数据存储麻烦且无法自动打印等问题,增加了该产品的生产成本,制约了企业的生产效率和效益的提高,不能满足现代大规模 的高效生产和检测的需要。此外,客户对产品功能的定制还存在多样化特点,故实现智能电动机保护器的自动检测有着重要的意义。
高精度电子元器件、现代单片机技术以及数据库技术的发展,使得自动检测智能电动机保护器成为可能。可以通过上位机控制整个检测过程,采用单片机技术实现信 号的产生并控制信号的通断,应用串口服务器技术控制多表位通信,借助远程服务器技术进行测试数据的存储等组成一个自动检测系统,以降低生产成本、提高了检 测效率、消除人工记录时易产生错误等弊端[2,3,4]。
123456下一页>
- 第一页:引言
- 第二页:系统基本要求
- 第三页:系统硬件结构原理
- 第四页:检测流程及软件
- 第五页:测试结果及分析
- 第六页:结 语
1系统基本要求
该系统需能自动完成对保护器各设定参数、数显精度、保护功能、附加功能等进行全面的检测,并且能自动判别检测结果是否符合产品技术指标要求,同时还应具有测试结果的存储、统计、查询以及检测报告输出等功能[5,6]。该系统主要需求和技术指标如下:
(1) 使用产品范围。适合各种不同规格的智能电动机保护器。
(2) 工作模式。全自动与单个检测项自动并存。
(3) 工作环境。鲁棒性强,能够应对流水线突然断电、人员误操作等突发情况。
(4) 检测效率。可同时检测多台相同规格的电动机保护器,并要求检测时间短。
(5) 功率源的技术指标。输出电压范围为:AC 3×30V~ 3×450V;输电流范围为:AC 0.1A~800A;移相范围为:0~360°;电压电流输出频率范围为:45Hz~65Hz;电压、电流正弦波输出时波形的失真度<0.5%;正 弦波输出时功率源的电压、电流、功率稳定度<0.1%;可以驱动阻性、感性、容性(<4uF)负载;具有内置的输出电压短路和输出电流开路自 动检测保护功能。
(6) 分机控制单元。能够与被检测保护器及上位机通信,能采集到保护器的开关量输入、模拟量输入,并具有开关输出控制和计时功能。
<上一页123456下一页>
- 第一页:引言
- 第二页:系统基本要求
- 第三页:系统硬件结构原理
- 第四页:检测流程及软件
- 第五页:测试结果及分析
- 第六页:结 语
2系统硬件结构原理
系统基本原理框图如图1所示。该系统主要模块包括:PC机,RS-485扩展通信模块,波形发生模块,电流、电压功放及切换装置,分机控制模块,打印机等。
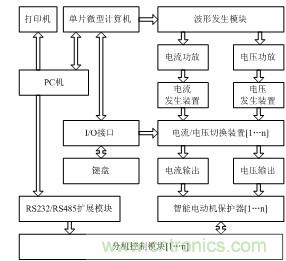
图1 系统基本原理框图
(1)PC机。PC机作用于上位机操作,主要实现人机交互功能,负责完成检测参数的设定、检测的启停控制、检测过程的实时监控、检测结果的保存与打印等工作,是完成整个检测过程不可或缺的设备。
(2)RS-485扩展通信模块。该模块主要完成PC机、波形发生模块、分机控制模块以及被检测保护器之间的通信。
(3)波形发生模块。波形发生模块(精密数字式信号源)产生检测中所需要的各类信号,通过电流、电压切换装置控制打开电流、电压输出,并最终流入智能电动机保护器中进行精度、保护、开关量等功能的检测。
(4)电流、电压功率放大器。系统功率放大器采用了PWM功率放大技术,并设计了电压短路过载,电流开路过载及快速限流保护措施,确保功率放大器长期稳定可靠的工作。
(5) 电流、电压切换装置。单台电流切换装置示意图如图2所示,该装置主要有短路继电器和输出继电器组成,能够有效的避免电流开路。通过短路继电器和输出继电器 之间的切换,可控制保护器输入电流的有无;通过选择短路继电器某一路或某几路闭合,可以得到单相电流或多相电流。单台电压切换装置示意图如图3所示,通过 控制继电器的断开闭合,来决定是否输入电压信号。
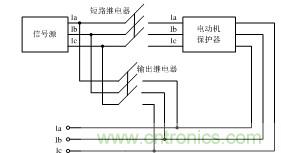
图2 电流切换装置示意图
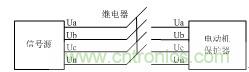
图3 电压切换装置示意图
(6) 分机控制模块。具有9路开关量输出,5路开关量输入,可以控制、检测保护器的开关量输入、输出状态;具有直流模拟量测量信号,范围为4-20mA,可以对 保护器模拟量输出进行检测;采用硬件时钟计时,精度为ms级,能统计故障的脱扣时间;拥有RS485通信接口,可与保护器、PC机间进行通信。
(7)打印机。用于打印检测结果,形成产品出厂检验报告。
<上一页123456下一页>
- 第一页:引言
- 第二页:系统基本要求
- 第三页:系统硬件结构原理
- 第四页:检测流程及软件
- 第五页:测试结果及分析
- 第六页:结 语
3检测流程及软件
智能电动机保护器自动检测系统软件主要包括下位机软件和上位机软件两个部分。下位机主要接收上位机的指令,完成对系统各部分硬件的实时控制,并实时采集系统中参数和变量。上位机主要实现人机交互、检测参数的设置、检测流程控制等功能。
3.1下位机软件
该系统控制模块的CPU为Cortex-M3内核的STM32单片机,用于各硬件模块的实时控制。下位机软件即单片机程序,其主程序流程如图4所示。系统 上电后,首先进行系统初始化,包括单片机的配置、I/O口初始化等,然后通过键盘或上位机输入不同控制命令,来完成对外部各种模块的控制。
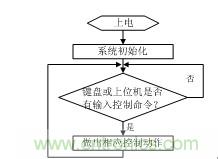
图4 单片机程序主流程图
3.2上位机软件
上位机程序流程图如图5所示。运行软件后,先输入对应分机单元接入的保护器序列号,系统会自动设定好检测参数;然后,启动检测过程直到检测结束。
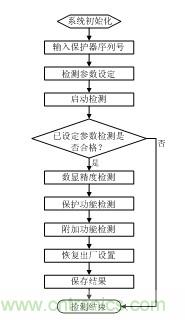
图5 上位机程序流程图
(1)已设定参数的检测。将被检测的保护器寄存器值读取并保存,然后将其与正确的配置参数做比较,合格后进入下一项测试,否则退回调试部门,待调试正确后方可进行其他项测试。
(2)数显精度检测。将信号源升到对应检测所需的信号,等待信号源工作稳定后,读出对应保护器的显示值,计算误差进行判断,结束此项精度检测。其中,在检测过程中启动报文确认机制。精度检测的流程图如图6所示。
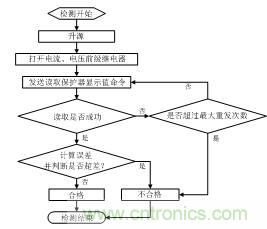
图6 精度检测流程图
(3) 保护功能检测。包括过载、断相、接地、剩余电流、堵转、阻塞、不平衡等功能检测,主要检测流程如图7所示。检测开始后,为了防止之前项检测的干扰,首先切 断电流的输入信号,然后根据检测需要,升起相应的故障信号,打开对应检测项的脱扣使能位,并屏蔽其他脱扣位。其中,为了防止保护器工作状态处于脱扣,影响 到检测结果,需对保护器进行一次远程复位操作,随后操作继电器,给保护器输入信号,同时对分机单元发送计时命令(该命令为广播包命令),此后不断的读取保 护器运行状态。若读到保护器为脱扣状态,则分机发送读取计时命令,获取脱扣时间进行判断是否合格;否则,在超过规定的最大设定不脱扣阈值后仍然不脱扣,就 判断该保护器该项功能不合格。
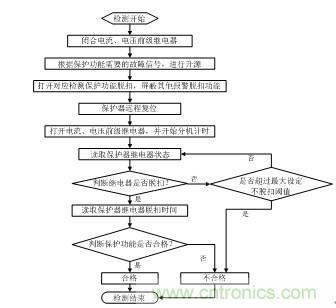
图7 保护功能检测流程图
(4)附加功能检测。根据客户的订货单,进行附加功能检测,主要包括:欠载、起动超时、短路、欠电压、过电压、欠功率、过功率、相序等保护以及故障记录和开关量。基本检测流程与保护功能检测相似,其中对于开关量的检测需要单个开关量依次检测,防止开关量之间的短接。
(5)恢复出厂设置。针对检测过程中对保护器参数的修改,在检测结束前必须要恢复出厂设置,保证保护器出厂时满足各项技术指标要求。
(6)保存结果。系统将测试数据与结果存入了远程服务器数据库中,利用存储过程来实现数据库的操作。数据保存结束后,检验人员可以利用上位机中的报表管理模块对出厂检验报表进行输出。系统的报表功能是通过企业级报表开发工具来实现的。
<上一页123456下一页>
- 第一页:引言
- 第二页:系统基本要求
- 第三页:系统硬件结构原理
- 第四页:检测流程及软件
- 第五页:测试结果及分析
- 第六页:结 语
4 测试结果及分析
该自动化检测系统经过不同规格型号的智能电动机保护器多次测试,结果表明:系统能够准确、规范、高效的完成检测过程。其中多台全功能保护器一次检测完成时 间为5min左右,较常规的手动检测,极大的提高了生产效率。某种全功能保护器的一次准确度检测结果与功能检测结果分别如表1和表2所示。
表1 准确度检测结果
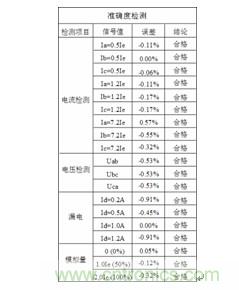
表2 功能检测结果
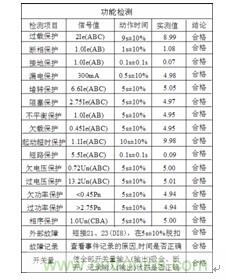
- 第一页:引言
- 第二页:系统基本要求
- 第三页:系统硬件结构原理
- 第四页:检测流程及软件
- 第五页:测试结果及分析
- 第六页:结 语
5结 语
智能电动机保护器自动检测系统具有人机界面友好、操作简单、自动化程度高等优点。检测结果表明,系统达到了预期的各项技术指标。在整个检测过程中,基本无 需人为干预,检测自动化程度高,最大限度地保证检测过程的规范性与测试结果的客观性。经测试,在自动检测模式下,多台全功能保护器完成整个检测流程需要时 间大大地得到了缩短。此外,该系统稍加修改即可用于其他仪表的自动检测,具有适用范围广等特性。