射线检测中CMOS的研究
中心议题:
- 射线检测中CMOS的研究
- CMOS探测器简介
- 检测工装设计
- 选用Canny边缘检测算法进行缺陷边缘定位
1 CMOS探测器简介
射线检测技术利用X射线探测材料内部的不连续性,并在记录介质上显示出图像。随着技术的不断进步,射线检测从传统的以胶片为记录介质的照相方法不断扩展,形成了多种数字化射线检测手段,如底片的数字化处理技术(Film Digitisation)、射线实时成像技术(Radioscopy)、计算机射线成像系统(Computed Radiography)和射线数字直接成像检测技术(Direct Radiography)等。实际应用中需要根据检测要求的分辨率和相对灵敏度选用合适的方法。相对于其它射线记录介质(如CCD、多晶硅等),CMOS(互补的金属氧化硅)技术更具有性能优势。目前,CMOS探测器的最小像素尺寸可达39μm,检测精度较高,温度适应性好,结构适应性强。
较之庞大的增强器成像系统,CMOS射线扫描探测器(图1)结构小巧,内部芯片集成度高。较之CCD成像方式,CMOS的每个探测点都有自己的放大器进行单独配置。CMOS在其内部通过转换屏将接收到的射线转换为光线,直接与转换屏接触的探测点单元将光线转换为电子,每个探测点单元有自己的放大器将电信号放大,最后在探测器内对信号进行A/D转换,形成二进制编码传送到计算机。CMOS主要适用于20~320 kV射线能量,80/μm的空间分辨率,无几何放大情况下检测分辨率为6 lp/mm,检测图像达到4096级灰度。
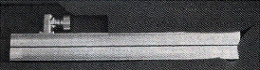
2 CMOS探测器的检测应用
2.1 检测流程
由于CMOS射线探测单元排成线阵列,静止状态下只能得到射线透过被检物体而形成的投影图像中的一条线。为获取被检测物体的图像,需要进行相对扫描运动,逐线采集并拼成完整的投影图像。获取检测图像时要求射线能量波动尽可能小且可长时间连续工作,因此笔者采用恒压式射线源(YX―LON MG325,最大电压320 kV,大焦点3.0 mm,小焦点2.O mm)。采用CMOS线性X射线扫描探测器进行射线检测的流程为:探测器配置及校准一确定透照方式,调节位置参数一相对运动,获取扫描图像一图像处理,缺陷分析。
2.2 检测工装设计
探测器的成像单元(线阵列)需要与射线束中心线良好匹配,不能出现相对位置倾斜和偏移等现象。因此,需设计合适的成像工装,以完成探测器的固定、位置调节及实现与检测工件的相对运动。工装要能方便地移入移出(筒形工件),应具有一定的灵活性和较大的适应性(检测不同类型工件)。
本着简便、实用的原则,在已有射线实时成像系统基础上进行检测工装设计,即检测时将检测工件放在载物台上,可实现左右平移、绕垂直轴旋转等运动;探测器通过工装固定于射线实时成像系统增强器运动轴上,可实现垂直升降和前后平动。另外,探测器还可实现一定角度的旋转调节。通过与实时成像检测系统的有机结合,可实现多种类型工件的射线检测。此外,应用时对于工件还要设计固定定位工装。
2.3 探测器配置与校准
首次使用探测器时需指定成像器类型参数(长度和可承受电压等),以便确定出可用的最小积分时间。在探测器正常工作前,必须对其进行配置与校准,以便在一定的成像条件下,使所有探测单元的偏置输出及增益输出达到一致。
对于新的检测对象,首先配置好采集图像相关的参数(积分时间、扫描精度以及是否迭加平均),然后开始进行探测器校准。校准时还要考虑焦距及物距的影响。一般校准时需进行三个步骤:①关闭射线源,探测器进行偏置校准。②开启射线源,调节到检测需使用的电流电压值,使探测器的线阵列输出信号达到最大但未出现饱和为止。③调节射线能量,使线阵列输出信号降低为最大信号的一半。校准的结果以文件形式存储,可供以后的检测调用。但调用后若再更改其中的校准参数,则需重新校准后才能进行检测。
对于大多数检测对象,在实际检测时应用的电流、电压值较高,在进行探测器校准时输出信号早已饱和。为解决这一问题,根据不同厚度的检测情况,设计了相应的校准用检测试板。试板厚度均匀,在校准第一步完成后将试板放在射线源窗口,然后开启射线进行下一步校准操作。
123下一页> 关键字:CMOS CCD成像 成像单元 缺陷定量分析  本文链接:http://www.cntronics.com/public/art/artinfo/id/80015034
2.4 透照方式选取
(1)平动方式适用于平板焊缝类工件的射线检测,检测时保持探测器与射线源位置相对固定,将工件放在载物台上,以合适的速度沿X轴平行移动。对于管、筒上的环形焊缝,如果采用平动方式成像,采集的将是椭圆形透视图像,只有中心区域的图像才可用于检测结果评定,并且需要旋转多个角度才能完成全部检测,降低了检测灵敏度(图2a),某些情况下由于厚度太大而不能实现透照检测。
(2)旋转方式要求调节相对位置使工件放在载物台回转中心,且与射线束中心、探测器中心处于一条直线上。对于筒形件,通过工装将探测器置于工件内部,尽可能贴近检测部位,采用单壁单影的方式透照;对于内径较小的管状与筒形工件,采用双壁透照的方式;旋转一定角度即可将透照区展开成像,可有效提高检测效率(图2b)。对于回转类工件,采用旋转方式成像具有突出的优点,可提高图像质量,缩短检测时问。
2.5 运动速度控制
由于探测器必须有相对运动才能成像,因此需要将运动速度控制在合理的范围。如果速度不合适,则得到的图像就存在拉伸或压缩现象。另外,分辨率越高、图像噪声越低,运动速度需越低。
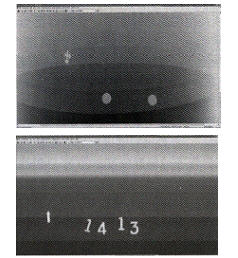
平动成像中的移动速度V与探测器的曝光时间T、成像精度P、透照放大倍数M和重复扫描次数N有关:

2.6 检测参数优化
最佳放大倍数Mopt与探测器的固有不清晰度Us、射线焦点尺寸d有关:

扫描图像的清晰度与重复扫描次数有关,图像扫描时采用Double Graylevel选项,类似于实时成像检测中的4帧图像叠加(N=4)。进行检测的速度降低了4倍,但图像却有比较大的改善,噪声明显降低,更有利于缺陷的检出与识别。检测图像能够满足GB 3323―1987标准规定的AB级要求。
<上一页123下一页> 关键字:CMOS CCD成像 成像单元 缺陷定量分析  本文链接:http://www.cntronics.com/public/art/artinfo/id/80015034?page=2
2.7 缺陷定量分析
在进行图像尺寸测量时,需要将经过计量或已知精确尺寸的试件紧贴在被检焊缝的一侧与焊缝同时成像。每次评定前,应作一次标定,缺陷测量时进行对比或通过公式将图像尺寸转化为真实尺寸。为此,设计了专用的测量评片用试片(图3),试片也可用于检测相对运动速度是否匹配。
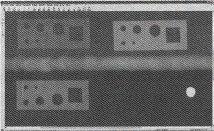
尺寸标定完成后,通过图像处理方法实现缺陷定量分析。选用Canny边缘检测算法进行缺陷边缘定位。接着对检测出的边缘进行细线化处理。然后通过搜索每条边缘线端点为中心的5×5或更大的邻域,找出其它端点并进行填充,完成边缘点连接,去除边缘检测图像中的间隙。再应用像素标记的方法,检查每一目标像素相邻点的连通性,进行闭合曲线内的目标标记。通过上述操作即可将不同缺陷标记出来以供测量用,最后完成缺陷参数计算。
2.8 图像存档管理
检测结果以数字图像形式存放在计算机上,为便于对检测图像进行统一管理,笔者自行设计了图像文件的管理数据库,记录检测信息(工件名、检测日期等)、成像参数和检测评定结果等。
3 应用结论及问题分析
CMOS射线探测器具有较高的空间分辨率(61p/mm,固有不清晰度<0.2 mm),检测灵敏度高(4096灰度级)。成像质量优于采用增强器的实时成像系统,接近或达到胶片照相的水平;在图像的对比度方面优于胶片照相方法和实时成像系统。
通过试验优化等方法,成功地将探测器应用于平板焊缝、环焊缝和纵焊缝等大多数产品零部件的射线检测,提高了检测效率,降低了检测成本。为更好地促进数字化射线检测技术的应用,有必要在下列方面开展研究工作:
(1)复杂工件的最优化检测及仿真[4],为检测结果的解释提供理论支撑。
(2)大容量图像文件的快速读取、处理及分析,缺陷定量分析的自动化、半自动化方法的研究。
(3)图像文件的管理、传输(引入PACS模式)[5]。
(4)建立新的数字化射线检测标准。<上一页123 关键字:CMOS CCD成像 成像单元 缺陷定量分析  本文链接:http://www.cntronics.com/public/art/artinfo/id/80015034?page=3